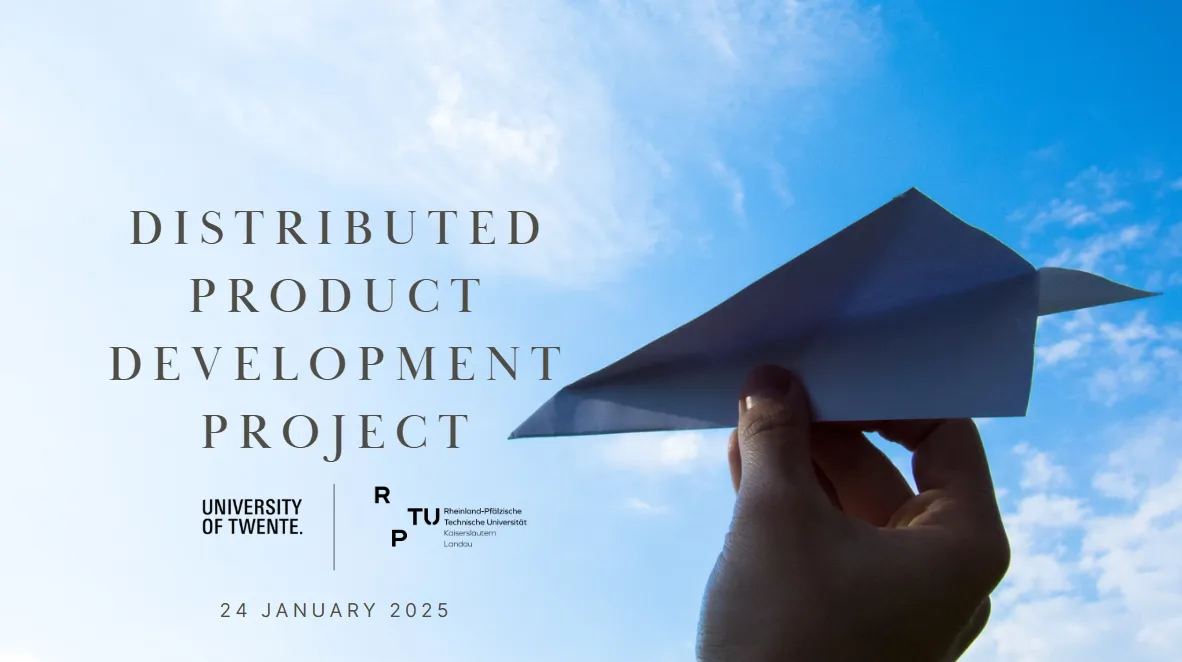
International Paper Plane Production Line: Digital Twin Development
international collaboration robotics digital twin industrial engineering automation
This was a project during my masters where we worked together with students from RPTU Kaiserslautern in Germany. The German team consisted of mechanical and software engineers, whilst we from Twente brought industrial engineering perspectives. We had one common goal: design a factory production line that could fold paper planes automatically.
The challenge was that we had different objectives. Our focus was on actually achieving a working physical production line, whilst the German students were developing a digital twin of our setup that would help us optimise and improve the line through simulation.
Project Structure
The production line was split into three distinct stages which, when placed behind each other, should have been able to produce paper planes continuously. Each stage had specific folding responsibilities and used Arduino Braccio robotic arms along with conveyor systems and sensors to detect paper position and manage the workflow.
Stage 1 handled the initial folds and paper positioning. We used light sensors to detect when paper was properly positioned and guide rails to ensure accurate alignment throughout the folding process.
Stage 2 focused on the middle folding operations with a more complex mechanism including a lowering system for precise fold creation. This stage proved particularly challenging due to the precision required for consistent fold quality.
Stage 3 completed the final wing folds using a sophisticated setup with multiple rollers and positioning systems. The complexity here was managing the partially folded paper through the final shaping operations.
Collaboration Challenges
Working with the German team presented interesting challenges around communication and goal alignment. Initially, we struggled to establish shared understanding of our objectives, as our team was focused on producing an operational prototype whilst they were optimising for throughput in their digital simulations.
The midterm presentation really turned things around. The face-to-face meeting in Enschede cleared up many assumptions and helped us understand each other’s perspectives better. From that point, we formed integrated working groups and established much better communication through Discord and regular video calls.
Technical Development
We modelled the entire system in OnShape, which proved excellent for collaboration since everyone could work on the same models simultaneously. The German students also introduced us to more structured simulation approaches which improved our testing methodology.
The prototyping involved extensive CAD modelling, Arduino programming for sensor integration and motor control, and mechanical assembly of all three stages. We used various sensors including light detection for paper presence, position sensors for the robotic arms, and developed state machines to coordinate the entire workflow.
Results and Learning
We didn’t quite achieve the continuous production line we’d hoped for, but learned a lot in the process. The project gave us valuable experience with international collaboration, different engineering approaches, and the challenges of integrating physical prototypes with digital twin simulations.
The collaboration felt like working in a professional environment where different teams have different objectives but need to work together towards a common goal. It was particularly valuable learning how to communicate technical concepts across languages and engineering disciplines.